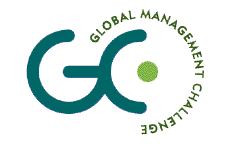
THE BUSINESS ENVIRONMENT
Your market
Your company operates in direct competition with a number of other companies that manufacture and sell the same products as yours, in the same geographic areas. You make three products, which are not specifically defined. They are three different, but related, types of consumer durables that the public think are generally desirable.
Your market consists of two geographic areas for traditional retail trade -
- the Euro-market - which is most of western and central Europe;
- the Dollar-market - which is the North America free trade agreement area (Nafta).
In all areas, you compete directly with the other companies taking part in the simulation, but additional competition also exists in the form of imports, or other local firms. Consequently, the market shares of the competing teams do not add up to 100%. This other competition, however, is not directly involved in the simulation.
ECONOMIC BACKGROUND
The population size and social make-up determine the underlying demand for products in each market area, and normal economic cycles of growth and decline can affect all markets.
Please note, however, that the economy in this simulation does not necessarily follow the present-day, real life economy; nor do real-life Government Policies have any bearing on it.
Superimposed on the general economic trend is a strong seasonal pattern of demand for the industry's products. This is not necessarily the same in all market areas, nor for every year, but the peak is usually in the fourth quarter.
Within the European market, trade is conducted in euros. In Nafta, trade is in U.S. dollars. Trade on the internet is in dollars.
All monetary decisions which you make will be in euros,
including decisions affecting Nafta and the Internet,
even though the final transaction may be in dollars.
The rate of exchange between the euro and the dollar will,
therefore, affect trading.
Economic statistics and reports will be issued during the simulation to help you assess economic trends and movements in exchange rates. These take the form of deseasonalised, official statistics for last quarter, for both the European market and Nafta, covering:
- Gross domestic product (GDP)
- Percentage unemployment
- Trade balance
- Central Bank annual base interest rates which will apply next quarter.
- Exchange rate of the euro against the dollar which will apply next quarter.
Limited information on some of these topics is also available about the rest of the developed world under Economic intelligence in your management report.
In addition, short extracts of political, economic and commercial commentary from newspapers will be given to help you forecast the way in which economies and markets are likely to move. You should decide how reliable this information is.
More (technical detail on exchange rates)
WORLD EVENTS
Significant 'world events' can affect all companies. These events may be the result of political upheaval, economic or environmental developments, wars, physical disasters such as volcanic eruptions or earthquakes, epidemic diseases, etc. They can have a serious effect on companies' operations, and also affect the product markets.
Externally, the level of disruption should affect all companies equally, but the level of internal disruption will depend on how well the company is able to cope with what happens. For example, a company that holds adequate stocks of materials and finished products may be able to continue to trade, but a company with inadequate stocks may find itself in difficulty.
These events may occur suddenly, and without warning, giving you no opportunity to react. It is more likely, however, that at least some information, taken from the press and appearing in the Business Report ahead of an event, will give some hint that it may happen.
It is important that you read all sections of the BUSINESS REPORT since they may contain important information about changes in costs (eg decommissioning charges) or other factors that are not necessarily fixed throughout the simulation.
You should bear in mind that, although this kind of disruption might not affect consumer markets directly, there could be an indirect effect on consumer confidence.
Note: although such world events may happen, it does not mean that they will happen.
MARKETING
Your company's marketing department is responsible for creating demand for, and selling the company's products successfully in the face of competition from rival companies. To do this successfully you must have a good marketing strategy.
In Europe and Nafta you sell through
agents
to retailers who, in turn, sell to the general public.
In those areas retailers are the prime target of your marketing effort.
You can also sell directly to the public worldwide through the internet to
people who have appropriate computer access.
Selling through the internet will also reach Europe and Nafta so that,
in a sense, you will be competing against your own agents in these areas.
Public demand will vary according to the economic climate
and the marketing effort of the competing companies.
The retailers and the general public are also the target of
direct competitors selling similar products in competition to yours.
Each product has a marketing image which you are seeking to promote in order to attract sales. This image is formed over time from a number of factors such as product quality, reliability, advertising, price and delivery which are of varying importance relative to similar factors in your competitors' products.
You decide some of these factors as part of your marketing plan, but others, such as the activities of your competitors, should be taken into account as you prepare the plan.
INFORMATION
To help you make forecasts, certain economic and competitive information about your competitors' activities last quarter is available to you, free of charge. This consists of the kind of information that would normally be freely available:
- Product selling prices
- Total number of employees
- Basic skilled wage rates
- Number of distributors
Apart from this free information,
you can decide
to subscribe to Audit Research, which monitors the sales of each product
and provides information about how the market is divided
between you and your competitors. This information costs
a fixed amount
each time you ask for it.
The information gives market shares by volume of sales
for each of the competing companies in:
- The European market.
- The Nafta market.
- The internet
You can also decide to commission research about your competitors' business activities and products. This information costs you a fixed amount every time you ask for it. It includes:
- Total amounts spent on advertising
- Total amounts spent on product development.
- A consumer assessment rating of the product design quality.
- A consumer assessment of the quality of your web site (if relevant)
PRICING
Each quarter you must review and decide the prices at which you will sell your products.
The price that you decide for each product is the amount you will charge your agents and distributors for each unit delivered. It is also intended as a guide to the retail price that should be charged. Your agents in the EU and distributors in Nafta make most of their profit from commission that you pay to them based on the value of orders and sales.
For internet sales, the price you decide is the price which the consumer pays (excluding any delivery charge).
The products are quite price sensitive, though not equally so, with relatively high prices leading to fewer orders and low prices yielding more. Price reduction, as a means of gaining more orders, only works up to a point - the public become suspicious of very low prices.
You set all prices in Euros regardless of where they are to be sold. Because Nafta and internet prices are decided in Euros, but passed to the end customer in dollars, fluctuations in the euro/dollar exchange rate will affect demand, and your ability to compete in these markets. You should, therefore, take into account exchange rates when fixing your prices.
If you decide not to offer a particular product for sale, enter a zero price on your decision form. You will then receive no new orders for that product from that market next quarter.
PRODUCT QUALITY
Apart from product design (see below) you decide the build quality of your products through decisions taken at production time. In general, the longer you allow your skilled workers to assemble each product, the better finish it will have, and the more reliable it will be.
You may unintentionally release to the public products with serious health and safety problems. Apart from the cost of physically putting things right, serious damage can be done to your marketing image, leading to loss of public confidence and consequent loss of orders.
You may also improve the build quality, and reliability, of your products by using premium quality materials, rather than basic materials. You can decide to use such materials to whatever extent you wish, product by product. Quality materials are also less likely to be a danger to the public. Premium quality materials are, however, significantly more expensive.
The more attention you pay to quality, the better your image will be, and the more products you should be able to sell. (See also the description of your quality control process).
Customers who find any products to be faulty can return them, under the company's guarantee, for repair or replacement. Obviously, the better their quality, the fewer product units will need to be returned.
Sub-contractors carry out repairs for you and invoice you for the work at an agreed cost.
Internet customers may also return faulty products to your distribution agent. A local sub-contractor repairs these products, under your guarantee.
PRODUCT DEVELOPMENT
An important way in which your products can be competitive is through developments in design and technology. Each quarter, therefore, you should decide how much to spend on product development for each of your products.
Regardless of how much you spend, you cannot assume that your efforts will be immediately successful. Product development is cumulative, so that the more you spend the greater the chance of making real improvements. A steady effort is most likely to be effective.
Each quarter, there are three possible product development outcomes -- When MINOR improvements are reported they will have been automatically incorporated into your products (without requiring any decision) and have a small but immediate effect on your product image and sales.
- MAJOR improvements that are reported may need further consideration, because the introduction of a major improvement renders existing models of the product obsolete. You may, therefore, wish to reduce existing product stocks, or build up marketing effort to introduce the improved product more effectively. You are therefore given the opportunity to decide whether to take up the improvement immediately or later.
- NONE means that your product development was not successful last quarter. Product development is a cumulative process, so this is not necessarily a bad thing. Following the announcement of a major improvement (see above) , your team starts on a fresh project which may take two or more quarters to come to fruition. The more you invest in product development, the shorter this period is likely to be.
Introducing improvements enhances your product image in the eyes of consumers, so that your consumer assessment rating - the number of stars awarded by product assessment panels - is likely to increase. If your development effort is too small, or has little success, then your products may become obsolescent, with a declining marketing image and a reduction in the number of stars awarded. If one or other of your products is found to be environmentally unsound, the accompanying bad publicity will usually lead to loss of stars.
The quality of your management will also affect the department's chances of success.
ADVERTISING
For each product, in each area, you should decide how much money to spend on advertising:
- on promoting sales of your products in the short term by providing television commercials, material for press advertising, and so on. This type of advertising has a limited effect on internet business.
- on promoting your company's corporate image in each area, regardless of product, in order to create long term confidence and goodwill. Corporate image advertising is cumulative, needing steady expenditure over a period to be effective. It not only extends the market for your own company's products, but also, combined with all advertising, tends to contribute to the general growth of the market. A strong corporate image is the main influence which persuades people to visit your web-site, so it is important for your internet business.
In addition to direct advertising, it is important for users of the internet that your web-site reflects and maintains your company's image. You can decide how much to spend each quarter on enhancing the efficiency and attractiveness of your site.
There is no precise information about the effects of advertising, except that it affects sales of products differently in different areas. Advertising in Nafta and the internet areas will also depend on the relative movements in the euro/dollar exchange rate.
SELLING
You can sell your products in two ways:
- To retailers in the EU and Nafta areas who then, in turn, sell to their customers.
- Directly to customers world-wide (including the EU and Nafta areas) via the internet.
European market sales agents
In the European market, you appoint agents who will act for you to sell and distribute your products. You have three decisions to make each quarter:
- The number of agents you want to represent you in the European market from the beginning of the quarter after next.
- The amount that you are prepared to spend on behalf of each agent, each quarter. This covers basic payments for sales aids, supervision and accounting, market research, etc. This includes a minimum quarterly payment for each agent, to cover certain administrative expenses. A decision to spend more than this minimum will allow your agents to cover a wider geographic area and improve selling on your behalf.
- The percentage you will pay your agents in commission on the value of orders received each quarter. Commission is your agents' main source of income. Higher commission will motivate them to sell on your behalf and will compensate them for the fact that the prices of products sold through the internet will tend to be lower than retail prices.
Because the European market is large, you may need several agents to provide complete coverage of the area. Their effectiveness will depend on the level of support you give them. The higher the commission they are paid, the greater will be their selling motivation, especially if you support them with an adequate level of advertising. You need to offer both reasonable support and commission if you are to successfully appoint and retain your agents.
Nafta distributors
The Nafta market is more difficult and costly to penetrate because of distribution difficulties. To reach this market you appoint distributors, each of whom have an established network of wholesalers. Three decisions are needed each quarter:
- The number of distributors you wish to act for you.
- The level of support payments you decide to make, per distributor, subject to a minimum payment to cover basic overheads. Support payments are intended to cover basic costs of handling your product. The efficiency of the operation on your behalf will increase as support payments go up but movements in the relative price indices and the exchange rate will also affect performance.
- The percentage you will pay to the distributors in commission on the value of sales made.
In general the same factors that motivate selling agents in the European market apply to distributors in the Nafta area. However distributors are not active sellers of your products. Instead they respond to demand created by your advertising. Commission is not intended to stimulate demand for your products, but contributes to the distributors' profit, and other variable costs. Again, you need to provide both adequate support and reasonable commission.
The internet
You can sell directly to consumers world wide through the internet. The number of orders you receive will depend not only on the usual marketing factors of price (plus delivery charge), advertising, quality and availability, but also on the attractiveness, ease of use and selling power of your web-site, backed by a strong corporate image. The function of short term advertising is to remind people of what is available on your web-site.
Four decisions are needed each quarter;
- the number of ports (this determines the capacity of your website)
- the amount spent on website development
- your distributor's support payment (see Table 3) - this will affect the efficiency of, and care given to your operation
- the % commission paid to your distributor on the value of sales (this will also influence your distributor's efficiency and care)
One problem with e-business is that consumer access to the internet depends on the general availability of computers, which is not universal. Another is that you will compete against your own products available through normal retail outlets. The advantages are that you are not dependent on middlemen to sell for you and that customers pay by credit card and therefore you get paid at the same time as the goods are delivered.
Order processing and credit card payments are handled for you by secure e-commerce software. Orders are then passed to a single distribution agent to be made up, packaged and delivered. The efficiency and care with which this is done will affect your marketing image so that poor service from your distribution agent will reflect badly on the company and its products. Conversely, prompt and efficient service will boost your image.
PRODUCT AVAILABILITY
Product availability affects the number of orders received, and the ability of your production department to keep up with orders is important. Completed products are delivered to agents' warehouses in the European market, to distributors in Nafta and to your internet distribution agent. All orders are intended for delivery as soon as possible in the same quarter in which they are received. Consequently you should try to keep an adequate stock of products available in all areas so that deliveries can be made promptly. Orders are only converted into sales when the goods have been delivered. Failure to meet orders received, will result in a queue of customers awaiting delivery, leading to dissatisfaction and lost sales, which will adversely affect your marketing image. The greater the number of orders outstanding, the greater this adverse marketing effect will be.
Product availability is even more important for trade on the internet. Goods for sale on the internet are sent to your distributor's warehouse from the factory for this purpose. If demand is greater than availability then potential customers are lost, and your company's image as an efficient internet trader will decline.
Important Detail
At the end of each quarter, at least half of any orders which remain outstanding in the European and Nafta areas will be cancelled by your potential customers, and those orders left for you to supply in the next quarter will be carried forward as a backlog to be cleared as soon as products become available.
If you decide to raise your price in the meantime, or to reduce the quality of your products in some way, then more of your backlog will be cancelled at the beginning of next quarter and the total number of orders cancelled will then be greater than half.
Should you decide to stop production of a product, any backlog of orders which you may have at that time will remain to be satisfied at last quarter's price.
Cancelled orders do not go directly to your competitors, but they will benefit in future quarters due to your poor delivery image.
On the internet, if there is a shortage of product, no further orders can be taken. Hence, although there can be no backlog, there is a negative effect on your image.
MARKETING MANAGEMENT
The whole of your marketing effort depends on good management. The amount you decide to allocate to your management budget will therefore have an important effect on the quality of your sales management, and hence on the success of your marketing effort as a whole.
Your company's selling effort has an indirect cost which covers the expenses of a sales office, and of supervising your marketing effort. This is calculated as one percent of the value of orders obtained in each quarter.
OPERATIONS
Your company's operations department is responsible for making, assembling and distributing the company's products as efficiently and cheaply as possible within the quality standards defined by your overall strategy.
The three types of product which your company sells are manufactured in your own factory, from one basic type of material. The products are made in two sequential processes:
- Machining, in which components are made on machines, each operated by four unskilled machinists. Shift working is possible in the machine shop. In addition, or alternatively, you can outsource components by ordering them from external subcontractors for delivery in the quarter after next (see subcontracting below).
- Assembly, in which the machined components are assembled into finished products and packed by skilled assembly workers, who only work single shifts.
Table 5 shows the material content of each product, and the minimum times taken to process one unit of each product through each of these stages.
Because of the differing space requirements of machines and assembly operations, you may need to consider the total production area needed for the mix of products you plan to make. Note that only a proportion of your total factory area can actually be used, because of the need for circulation and access space etc.
The number of products that can be made in your factory in any quarter depends either on the number of available components (whether machined in your own factory, or outsourced), or on the capacity of your assembly shop to assemble these components, whichever is the lower.
A lack of materials will never limit your production capacity, because any shortfall is purchased automatically on the spot market, although at a premium price (see below).
MACHINING
The capacity of your machine shop, in terms of productive hours, depends on the number of machines that you have in your factory (see Capital expenditure), and the shift level which you decide to operate, diminished by the number of hours lost through breakdowns and slower machine speeds due to ageing.
Catastrophic machine failure can also seriously reduce production time for more than just a few days, while the machine is brought back into production. If this lost time leads to a loss of sales, incurring backlog, the value of lost sales can be recovered from your insurance company. The cost of such repairs can also be recovered.
For each level of shift working there is a maximum number of hours each quarter available for production from each machine.
Important Detail
The machining times, given in Table 5 are for producing a set of components ready to be assembled into the finished product. These are the times expected from 100% efficient, new machines. As machines get older, or are used more, they become less efficient, and take longer to make the components for each product.
The introduction of a preventive maintenance programme (see below) can slow, or even reverse, this process of deterioration, but eventually each machine will reach a level of inefficiency at which it may be better to sell it and replace it with a new one. A further consequence of ageing is that a machine will tend to break down more often, and productive hours will be lost until it can be repaired.
Your insurer's assessment of lost sales first considers Product 3 in the EU, then Nafta and finally the internet; then Product 2 and finally Product 1, until all lost sales specifically attributable to loss of machine capacity are covered.
PLANT MAINTENANCE
You employ specialist independent contractors to carry out maintenance on your machines. Each quarter you decide how many hours of planned maintenance per machine you wish to contract out.
There is a fixed cost per contract hour for each machine which covers labour, spares, materials, tools and supervision.
The first priority of the maintenance effort will be to repair broken down machinery, any hours left over within the contract will be used on preventive maintenance outside normal working hours.
When there is a catastrophic machine failure, your normal maintenance contractors carry out repairs in the usual way. The cost of this work (which may need to be done at the emergency rate) can then be added to your quarterly insurance claim provided that you have the appropriate insurance.
The more preventive maintenance you are able to do, the fewer breakdowns there will be, and if a breakdown does occur the shorter the time before the machine is back in service again. Preventive maintenance also slows the rate at which machines become less efficient.
If your allocation of hours to contract maintenance is not even sufficient to cover basic repair times, any additional hours needed to meet this primary effort will be charged at a higher rate per contract-hour.
SUBCONTRACTING
You can decide to outsource some, or all of your machining work to external subcontractors in addition to, or instead of, machining components in your own factory.
However, any subcontracted components that you order next quarter will not be available for assembly next quarter, but will be delivered to you in the quarter after next. You can then assemble them, along with any components machined in your own factory.
The current price of materials, your decisions about the use of premium materials, and the exchange rate, will determine the cost of any outsourced components. The cost range for each product is shown in last quarter's management report, but the actual cost will depend on the percentage of premium materials used.
In fulfilling your production schedule, your operations department will use any outsourced components first. If required, machining will then be used in order to complete the schedule.
Any components that remain after your production schedule is completed, will be held in stock as 'work in progress', to be assembled later. Such stock is valued at purchase cost.
If you have sufficient space,
you will hold such work in progress stocks in your factory.
If not, you will need to store them in external warehouses at
a cost shown in Table 13.
ASSEMBLY
As well as being limited by your machine capacity (or bought-in components), your factory's output also depends on the ability of your skilled workers to assemble the components into finished products.
Each product has a minimum assembly time but, as part of your marketing policy (see above), you should decide the actual times to be taken. The longer the assembly time, the better the quality of your products will be (up to a point).
Having decided the time that it should take to assemble one unit of each product, the number of each that you can make, and the product mix, will then depend on the number of skilled workers that you employ, diminished by absenteeism and industrial unrest.
Assembly workers work only on a single, day shift, up to a maximum number of hours per quarter. There is no limit to the number that you may employ, provided that you can recruit them and that you have enough space for them. After allowing for the area taken up by your machines (see Table 26) the remaining factory area may limit the number of assembly workers that you can usefully employ.
Your assembly workers are prone to serious accident like any one else, both at work and at home. Prolonged absence can seriously affect your production schedule and could lead to loss of sales. When this happens, temporary assembly workers are brought in from an agency service, which charges twice the hourly wage rate paid to your own workers. Meanwhile, you continue to pay your own employee who is off sick.
If you are insured (see later) then these additional costs can be recovered through the company's insurance claim.
You could also try to improve motivation, reduce absenteeism, and improve safety by spending more on management and staff training.
PRODUCTION PLANNING
Each quarter, you decide the number of each product that you plan to deliver to each area. This delivery schedule is the main set of decisions that concerns the operations department.
Normally the number of each product actually produced will be those scheduled to be delivered plus those which have had to be re-made because the original was rejected as defective, either at the assembly stage or the inspection stage in quality control.
Apart from labour and material costs, which are discussed elsewhere, there are certain other semi-fixed costs which are charged to your operations department. These are:
- a cost per shift for supervision;
- a cost per machine for production overheads;
- a charge per machine hour for running costs;
- a production planning charge for each unit to be delivered.
Important Detail
If your production schedule is too ambitious because you have insufficient machine capacity (and work in progress) or skilled labour, then production will be limited to whatever quantities you can make. Quality control will reject any sub-standard products and the remainder will be delivered in proportion to the number asked for in your original production schedule. When your production schedule is cut back in this way you will find that where your decisions are reproduced in the Management Report for next quarter, the affected numbers will be starred (*).
Any stock of product left unsold in an area at the end of a quarter will be kept in the warehouse to be sold in the next quarter. You can decide, however, to return excess stock from your internet distribution agent or European selling agents for redistribution to other areas, by specifying a negative quantity on the Decision form. Goods cannot be returned from Nafta.
You cannot deliver products to areas where you have no agent. Such decisions will be set to '0'.
Rejects found in the production process are sold as scrap, and reduce the number of product units available for delivery, though if you have sufficient capacity, extra products to replace those rejected will be produced automatically, so that deliveries can be completed.
QUALITY CONTROL
Your quality control department inspects products during the manufacturing process. The cost of inspection per unit is shown in Table 10.
Inevitably, some products will develop faults after they have reached the customer and be returned under the terms of your guarantee (see above). The servicing of products returned under guarantee in the EU and Nafta is carried out in those areas by local service agents, who charge you (at fixed rates) for the work carried out. Products returned to your internet distributor are repaired locally by a sub-contractor at the same rates (including delivery).
It is possible that your products are delivered with unsuspected design faults, or be made from sub-standard materials, so that they become a danger to members of the public. If this happens, products are returned under guarantee for repair in large numbers, and you also require to examine and repair all units of product currently in the distribution system. This work is done by the normal repair contractor, who (because of the volumes involved) charges 75% of the normal fee per unit repaired. The additional cost of repair work done under an incident of this kind is added to your company's quarterly insurance claim for settlement by your insurer.
Your product reliability (and also the number that will be returned for repair under your guarantee) depends on the time that you allow your skilled workers for assembling the products, how well trained and motivated they are, the quality of the materials you use, and also the effectiveness of your quality control management.
DISTRIBUTION
You decide the number of products to deliver to the EU, Nafta and to your internet distribution agent (unless your production resources limit your ability to manufacture these quantities). Products are delivered to warehouses controlled by the agents and distributors, who make a charge for storage.
When in your distribution system, units of finished product can be lost, stolen or broken so that they do not reach their final destination in usable condition and have to be written off. Depending on the level of stock in your warehouse losses of this kind can lead to backlog and loss of sales. If you are unable to meet orders because of a loss of product, your insurer is prepared to cover the full sales price of all sales lost providing you have adequate insurance. If you simply lose stock but have no loss of orders (because you have sufficient stocks), you just receive the valuation of the stock lost (Table 21).
Journeys to your internet distributor and to the port used for shipment to Nafta, are of a fixed length. Nafta distributors are responsible for transport from the port in America. Journeys to Europe are made as round trips and depend on the number of agents you have selling for you.
Transport is by standard sized containers and mixed product loads can be carried, but part loads are charged at the full load rate.
Important Detail
Hired transport has
an all-in cost per day
for the container and transport costs.
The total cost of delivery to your internet distribution agent and
to Nafta distributors will depend on -
- the number of loads to be delivered - which is determined by
- the number of products you specified for delivery and
- the container capacity (in product units),
- the fixed journey length and
- the maximimum distance that can be covered per day
Finished product units are warehoused in the European market (including products for the internet distributor) and Nafta at a cost per unit, based on the average quarterly holding. Warehousing in Nafta is charged in dollars and converted to euros at the rate quoted in last quarter's management report.
MATERIAL PURCHASING
All three products are made from the same basic materials, but the material content varies product by product. Furthermore, you may decide to use a proportion of premium quality materials for any, or all of your products.
You decide how to buy basic materials. You can buy them at the current spot price for delivery next quarter, or on the Futures Market for delivery in three months' or six months' time. Prices for each option are quoted in last quarter's management report.
Materials ordered for future delivery incur no storage charges, but all material becomes your property from the time it is ordered, and is valued on your balance sheet. Once material is delivered you may have to pay storage costs (see below) if there is insufficient space in your factory after allowing for the area occupied by your machines and assembly operations.
Premium quality materials are purchased from suppliers who deal in superior, environmentally friendly, materials. The price for such materials is a fixed percentage above the spot price. Deliveries of premium materials are made on a 'just-in-time' basis to meet your production schedule and, therefore, do not need to be held in stock. You decide the proportion of such materials to use, product by product.
Important Detail
Material ordered next quarter is invoiced next quarter, based on prices quoted in dollars last quarter. The equivalent amount in euros is then paid in two parts. 50% immediately and 50% in the following quarter. No adjustment is made for a change in the exchange rate between these part-payments. The second part of the payment is carried forward in the balance sheet as part of creditors until it is paid in the quarter after next.
If your production plan requires more materials than you have available for next quarter, then sufficient additional materials are bought automatically on the Spot Market in order for you to complete production. Such emergency purchases are at a premium over the normal price.
Your buying and warehouse department incurs a fixed administrative cost per quarter.
Material is stored in covered space in your own factory, if possible. There is no specific cost for maintaining your own storage area other than the fixed administrative cost (see above).
The space available depends on the area of your factory and how it is being used (see Table 26). If there is insufficient space, then the excess materials must be stored in commercial warehouses nearby at a quarterly rate per unit, based on the average quantity held.
INTERNET WEBSITE
An Internet Service Provider (ISP), who sells you web-hosting capacity, provides you with access to the internet. If you wish to trade over the internet, your website should have the capacity to cope with the volume of traffic that it might attract. This capacity is defined in terms of the number of access "ports" it has.
You decide the number of ports that you want to operate, but any change requires one quarter's notice and, therefore, will not be fully effective until the quarter after next.
Demand on your web-site will vary from day to day, and also throughout the day, so that deciding how many ports to install is not straightforward. If you are not able to give quick and efficient service to visitors at peak times your marketing image may decline quite sharply. The management report for last quarter shows three statistics which may be helpful:
- The capacity of your system, as decided, in terms of its number of ports
- The number of visits made to your web-site last quarter.
- The percentage of potential visits to your site that failed due to poor capacity.
Your website incurs a quarterly cost. This includes a cost per port, and a volume cost to pay for secure trading and credit-card handling. The total quarterly cost is treated as a marketing expense and is paid to your ISP in the same quarter.
Software determines the quality of your website (attractiveness, ease of use, etc.) and you decide how much to spend on website development, which is mainly for such software.
Regular, independent surveys give "Star Ratings" which show how customers rate your web-site. Five stars are the best possible; one star is the worst. Such information incurs an additional cost.
MoreOPERATIONS MANAGEMENT
Good management affects the whole of your operations. The amount that you decide to allocate to your management budget will therefore have an important effect on the quality of your operations, and hence on the success of your ability to meet demand.
PERSONNEL
Your personnel department is responsible for ensuring that the company has sufficient employees to function effectively. Workers must be recruited in a competitive labour market, within which people can move from company to company seeking the best terms and conditions. The supply of people in the labour market can significantly affect your company's ability to operate efficiently.
The company's labour force is divided into four sections:
- Unskilled machine operators - who make the components for the company's products.
- Skilled workers - who assemble completed products from the machined components.
- Ancillary workers - storepeople, clerks, junior management, etc.
- Senior management.
All grades of workers may leave because of retirement, sickness or in order to work for rival companies. Workers who leave do so at the end of a quarter.
In order to meet your delivery schedule, you need to recruit employees in sufficient numbers to cope with your production needs and to counteract the loss of any workers retiring or leaving to work for other companies.
Your personnel management task has two specific aspects - recruitment and motivation.
In the simulation, ancillary workers are dealt with in the context of their own departments and their costs are linked directly with departmental costs. You do not need to make any decisions about them.
Senior management is dealt with below.
RECRUITMENT
Assembly Workers
Skilled assembly workers are the product of intensive training and may be difficult to recruit.
You decide how many assembly workers you wish to recruit (or dismiss). Recruitment is either from the pool of unemployed skilled labour, or from other companies who employ skilled workers. Note, however, that recruiting is not always successful - you may not get any!
Effective recruiting depends not only on current earnings, but also on motivation, the quality of goods which you produce, and the ability of your personnel management.
It also depends on the number of unemployed available in the labour pool. In periods of full employment, recruitment can be very difficult, and trying to tempt people away from other companies may lead to a very unstable labour market.
Alternatively, in order to acquire a small number of assembly workers, you may decide to train unemployed unskilled workers. Although more expensive than recruitment, training is more certain.
Whether you decide to recruit or train, the new employees will not be available for production until the quarter after next. Furthermore, you may be limited by the space available in your factory for more assembly workers (see Table 26). If this is insufficient, then your decisions will be reduced to a level that is possible (this could be zero).
Unskilled Machine Operators
Four unskilled machine operators are needed to operate each machine on each shift that you work. Any change in the number of machines you have, or in the level of shift working, will mean that more or fewer unskilled workers are needed.
As with assembly workers, unskilled workers may leave if they feel that working conditions in your factory are not as good as can be found elsewhere.
Because there are always unskilled workers available in the local pool of unemployed labour, any need for new or replacement people is handled automatically at a lower level of management in the company, and senior management is not involved. The shift supervisor will always be able to recruit enough workers from the pool of unemployed, at the start of next quarter.
More (important detail)STAFF TRAINING
In addition to training unemployed unskilled workers to become assembly workers (as described above), you may also decide to provide your staff with general skills training in order to improve their motivation, teamwork and effectiveness.
External consultants provide such 'on the job' training which can have both immediate and long-term benefits for your company. The results of such training, however, can be variable.
The training is measured in consultant days, and charged at a rate per day (see Table 15). Typically, a consultant can provide training for about 5 to 10 employees each day.
PAY and CONDITIONS
As well as ensuring that you have enough workers, your personnel department should also manage the cost of the workforce. Although you decide the wage rate, the way in which your workers are treated can also have a significant effect not only on motivation, but also earnings. Overtime, and shift payments can be controlled to keep costs down, but these elements can only be managed effectively in the context of current economic conditions, and your marketing and operations strategy.
Assembly Workers
Skilled assembly workers are paid at a basic hourly rate, which you decide each quarter. This basic rate is subject to an agreement with the trade union which does not permit wage rates to be reduced. Any increase in the basic rate is implemented at the beginning of next quarter.
Machine Operators
You can change the capacity of your machine shop by installing more machines, selling existing machines or by changing shift levels (see machining above). Changes of these kinds will directly affect working conditions and pay.
Ancillary Staff
The cost of other workers in your company is included in the various costs associated with the departments in which they are employed. These include: clerical and accountancy staff, buyers, warehouse staff, researchers, etc.
SENIOR MANAGEMENT
Your team assumes the role of the company's Board of Directors and can consist of a Chief Executive, and executives who are responsible for Marketing, Operations, Personnel and Finance. You decide a management budget which is spent on outside services and expertise, directors' salaries, and general management expenses. The management budget influences the general quality of management and this, in turn, affects efficiency in all parts of the company.
More (important detail on pay)FINANCE
Your finance department is responsible for ensuring that the company's funds are managed efficiently in line with corporate strategy. This implies a variety of roles which include monitoring profitability, controlling investment and borrowings, and managing the company's assets and dividend policy. Above all, it must work closely with the management team to maximise the company's investment performance, the criterion by which you will be judged.
SHARES
The company is financed by shareholders' capital, consisting of shares with a nominal value of €1 (euro) each, to the amount shown on the company's balance sheet.
The company's shares are quoted on the Stock Exchange, and the latest share prices for all companies are quoted each quarter in your management report. Many different factors determine your share price.
You can decide to:
- issue more shares
- or repurchase (and cancel) shares from the market
There may be other restrictions that apply to share issues and repurchases. For example, share issues and repurchases are not allowed if the share price is below par value (€1).
DIVIDENDS
Each quarter you should decide the rate of dividend to be paid to your shareholders. This is expressed in cents per share (or as a percentage of the share capital).
Good dividend payments are an important element of your investment performance. Many shareholders look for capital growth from an increasing share price but others, including major institutional investors such as pension funds, value a consistent stream of dividends.
Dividend payments are made at the beginning of quarters. The total dividends paid next quarter may not exceed the company's retained earnings as shown in your balance sheet for last quarter. If you try to pay a dividend that exceeds your retained earnings, the dividend rate will be restricted to what is possible (this could be zero).
TERM DEPOSIT
If your company has spare funds, then you may decide to place them on deposit for a period of 3 months. Term deposits earn interest at the current EU bank rate and such interest will be credited to your bank account at the end of next quarter.
By default, any term deposit will be 'rolled over' next quarter for a further 3 months, unless you decide to change the amount. Such deposits will be taken from, or credited to, your bank account at the beginning of next quarter (see more detail).
If you wish to reduce (or cancel) your term deposit, then you should enter the appropriate negative amount.
BORROWING - Term Loans
You can decide to take out, or add to, a long term loan at a fixed interest rate. In this type of loan the money comes from investment institutions that are prepared to commit themselves to your company for the long term, and become part of the funding structure of your company. Your company's borrowing power, as shown in last quarter's management report, may limit (or prevent) any new term loans.
The money is credited to you immediately at the beginning of next quarter as cash, or used to repay all or part of any outstanding overdraft which you may have - see below.
BORROWING - Overdraft
Finance is also available from a bank overdraft (i.e. a flexible bank loan) at an interest rate related to the current European Central Bank rate.
Your bank sets a maximum, authorised overdraft limit for next quarter, based on your company's short term assets and liabilities as shown in last quarter's balance sheet. Overdrafts are issued and repaid automatically as your cash requirements dictate.
If you need more funds than your overdraft limit permits, your bank will still continue to fund your company, but without security, by means of an unauthorised overdraft.
The interest rate charged on an unauthorised overdraft is much higher. Furthermore, this higher rate will apply to the whole overdraft, and not just the excess over your authorised limit.
In this simulation, bank loans will continue to be granted to your company even though, in normal circumstances, you might be considered to be insolvent.
No one is declared bankrupt in the simulation, even if your shares become worthless.
CAPITAL EXPENDITURE - Property
The company's factory (land and buildings) is wholly owned and has a value as shown in your company's balance sheet. No depreciation is charged on land or buildings.
Your management report shows both the area of land you own, and the effective floor space in your factory. Office space is mainly at the front of the building on an upper floor and, therefore, does not impinge on the total production space available.
You can decide to extend your factory (in order to provide more space for machines, assembly workers and stocks of material or work in progress), subject to the limitation of enough land being available, after allowing for access and parking (see Table 26). Such work is also subject to your financial position.
Using information from last quarter's balance sheet, your building contractor checks your credit-worthiness. If this is at least equal to the total cost of the planned extension, then the building work can go ahead. But, if your credit-worthiness is insufficient, then the contractor will only agree to extend your factory by some smaller amount (which may be not at all).
New building work takes nearly one quarter to complete, so that extra space only becomes available starting in the quarter after next. However, any new machines purchased next quarter can be installed at the end of the quarter (see below). The current cost (per square metre) of new building work is shown in your management report.
CAPITAL EXPENDITURE - Plant and equipment
You can decide to buy new machines, at a fixed cost. You may not be able to place orders for some or all of the machines you require unless your company's financial position is sound and you have enough space in your factory.
The machine supplier checks your ability to pay from your credit-worthiness, which may be reduced by the cost of any building work (see above). If your credit-worthiness is at least equal to the total price of the machines you want, the supplier will accept your order, together with your payment of the purchase price. If your credit-worthiness is insufficient, then the supplier will only take orders for that number of machines which your credit-worthiness covers (which may be none).
Machines that you buy next quarter are delivered and installed at the end of next quarter. They become available for use in the quarter after next.
The value of a machine is depreciated quarterly, by the decreasing balance method.
Each installed machine occupies an area of your factory. This includes the space needed for access and temporary storage of materials and machined components.
When you decide to sell machines, the oldest are sold first, at the start of next quarter, at their depreciated (book) value last quarter. However, because of new legislation on environmental issues, the potential for contamination and the need for safe waste disposal, there is a decommissioning charge whenever a machine is removed for sale. Any decommissioning costs are included under 'Other costs'.
Furthermore, because of the need for decommissioning, the space vacated on removal will not become available for other uses until the quarter after next.
INSURANCE
Your company's activities are at risk from a variety of random events which can disrupt its operations:
- Some or all of the materials held in your own warehouse may be accidentally destroyed by careless handling, theft, flooding or fire.
- Similar risks can destroy all or part of stocks of material in transit or in your own local warehouse.
- Key assembly workers, can suffer from serious home or workplace accidents which might disrupt your production capacity.
- Machines can suffer from catastrophic breakdown which takes them out of production for periods of time.
- Badly designed products can be distributed or sold which later are found to be environmentally dangerous, and need to be withdrawn for modification.
To guard against such incidents, you can decide to take out insurance which will cover any financial loss caused by them. Your insurance company has four plans in which the proportion of primary risk which your company takes on itself rises successively. Premiums are calculated as a percentage of the value of your non-current assets and inventories.
A fifth option is to take out no insurance at all, in which case you are exposed completely to the dangers and consequent costs of random disruption.
The other factor affecting the risk of random disruption will be the level of your management budget (Decision form). Good management leads to safer working environment, ensures that Health and Safety procedures are properly implemented and that your products are properly designed. Poor management tends to lead to a high-risk company.